Henkel Balti does not make compromises at the expense of the environment
In 1978 Makroflex brand name was established in Finland. Today it is one of the best-known building material trademarks in Europe. At their factory in Pärnu, Estonia Henkel Balti produces around 55 million cans of polyurethane foam and 18 million cartridges of silicone sealants and bitumen every year. Even though the production volumes are high, Henkel Balti pays attention to every single factor that determines the using convenience of the final product.
Today Henkel Balti (previously Henkel Makroflex) is part of the Henkel Group. Their aim is to “Achieve more with less” – to create more added-value products while reducing production footprint as much as possible. Product development chemist Karin Viipsi says that reducing company’s environmental impact can only be a result of several simultaneous activities. “It is well-known that controlling and optimizing production process reduces waste generation,” explained Viipsi.
Innovative technology helps to ensure the best quality
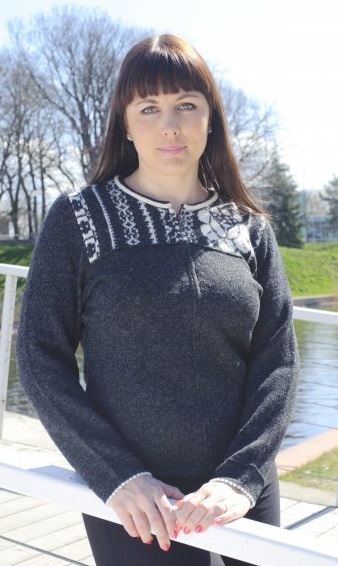
Waste reduction is one of the aims that Henkel Balti has in the international project LIFE Fit for REACH. In the project Henkel Balti is among five other Baltic companies that work towards reducing emissions by substituting hazardous chemicals and using resources more efficiently. In frame of the project, the Henkel Balti factory in Pärnu will start using infrared spectroscopy which allows examining and identifying chemical compounds. That in turn will help to enhance the control of raw material prior to production.
“The use of new technology means that we can be sure of the quality of raw material before it goes to the production line. That way we can decrease the number of defective products, but also generation of waste in general,” clarifies Karin Viipsi.
Viipsi points out that due to the implementation of the REACH regulation in the European Union, the issue of hazardous chemicals has been highlighted by industries. The purpose of the regulation is to improve the protection of human health and the environment from the risks that can be posed by chemicals, while enhancing the competitiveness of the EU chemicals industry.
This is actually something that Henkel Balti has been working on for years already. Over time, they have replaced lacquer gas and toluene with less hazardous solvents. Moreover, Henkel Balti has also substituted and reduced the use of fluorinated greenhouse gases. However, the work with substituting hazardous substances with safer alternatives is ongoing. For example, at the moment they are trying to find an alternative for methylene chloride, which is used as a cleaning agent in the production process.
Healthier products
Environmental and health principles are important not only in the production process. Henkel Balti ensures that their end-products have as safe ingredients to consumers and the environment as possible. The percentage of chloroalkanes, which are hazardous to the aquatic environment, is kept as low as possible. For example, Makroflex has a series of Power Foams in which free isocyanate proportion is close to zero, thereby it is safer for human health.
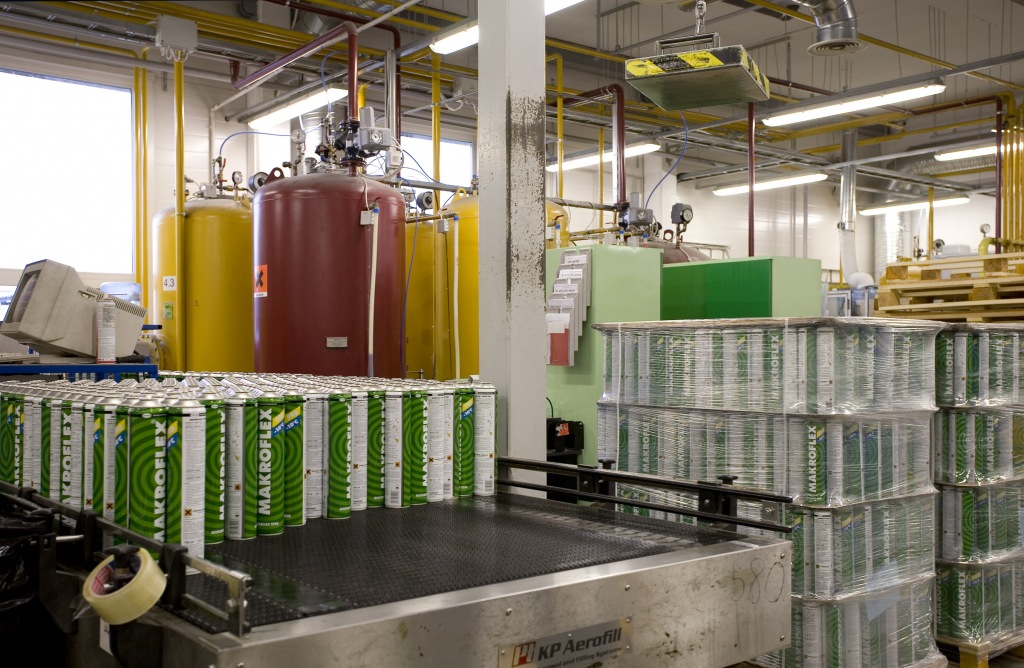
Another way Henkel Balti is reducing their environmental footprint is by investigating how to reuse their production residues. They are actively looking for ways how to reduce the waste coming from the production of polyol mixtures, isocyanates and polyurethane foam. Already today production residues are partially reused in their own production process. Also, Henkel Balti is trying to find companies that could use the residues in their own manufacturing processes.
Innovation has its own price
“Any kind of innovation requires, of course, extra investments, which additionally can lead to a general increase in costs,” says Karin Viipsi. That is the case with Power Foams’ series – even though the product itself is better for human health and the environment, it requires more energy for production and the process itself is slower.
Although today’s competitive advantage is still largely determined by the quality and price of the product, Viipsi believes that searching of resource-efficient solutions should be the everyday goal of each company.
According to Henkel Balti’s experience, in the case of general building materials, environmental sustainability is not so important for consumers. However, more attention is already being paid to ingredients of finishing materials.
The Henkel Group is part of the Together for Sustainability (TfS) network. Their purpose is to develop and implement a global audit program to assess and improve sustainability practises within supply chains of the chemical industry. Each supplier is surveyed and evaluated annually based on environmental, social, ethical and supply-side aspects. As already mentioned, Henkel Balti aims at creating more value for consumers but at the same time also reducing company’s environmental impact.